When it comes to precision woodworking, the details matter immensely. Among those crucial details is your choice of table saw blade—particularly its kerf width. The thinnest kerf table saw blades have revolutionized how woodworkers approach their craft, offering advantages that extend far beyond simple cutting. Whether you’re a professional cabinetmaker or a weekend DIY enthusiast, understanding the nuances of thin kerf blades can significantly impact your projects’ quality, efficiency, and overall cost.
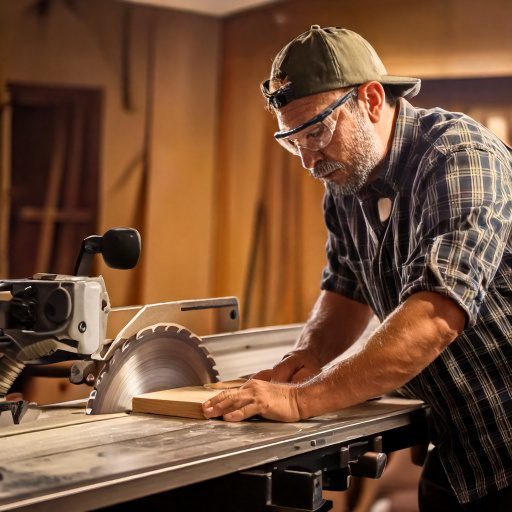
In this comprehensive guide, I’ll walk you through everything you need to know about thin kerf table saw blades—from the basic concepts to the finest options currently available on the market. Let’s dive in and discover how these specialized tools might be the game-changer your workshop has been waiting for.
Understanding Kerf Width and Its Importance
Before we explore specific products and recommendations, it’s essential to understand what we’re talking about when we discuss kerf width.
What Exactly is Kerf Width?
Simply put, kerf width refers to the thickness of the cut a saw blade makes as it passes through the material. It’s essentially the amount of material that gets removed and turned into sawdust during the cutting process. When you look at a table saw blade, the kerf width is primarily determined by the thickness of the blade plus the set or spread of the teeth.
Standard table saw blades typically have a kerf width ranging from 1/8″ (3.2mm) to just over 1/10″ (2.6mm). By contrast, thin kerf blades generally measure between 0.059″ to 0.094″ (1.5mm to 2.4mm). Ultra-thin kerf specialty blades can go even thinner, with some measuring just 0.047″ (1.2mm) or less.
To put this in perspective, imagine cutting twenty boards with a standard kerf blade versus a thin kerf blade. With the standard blade, you might lose nearly 1/4″ of material to sawdust, while the thin kerf blade might waste only half that amount. Over multiple cuts, this difference becomes significant.
Why Thin Kerf Blades Matter in Woodworking
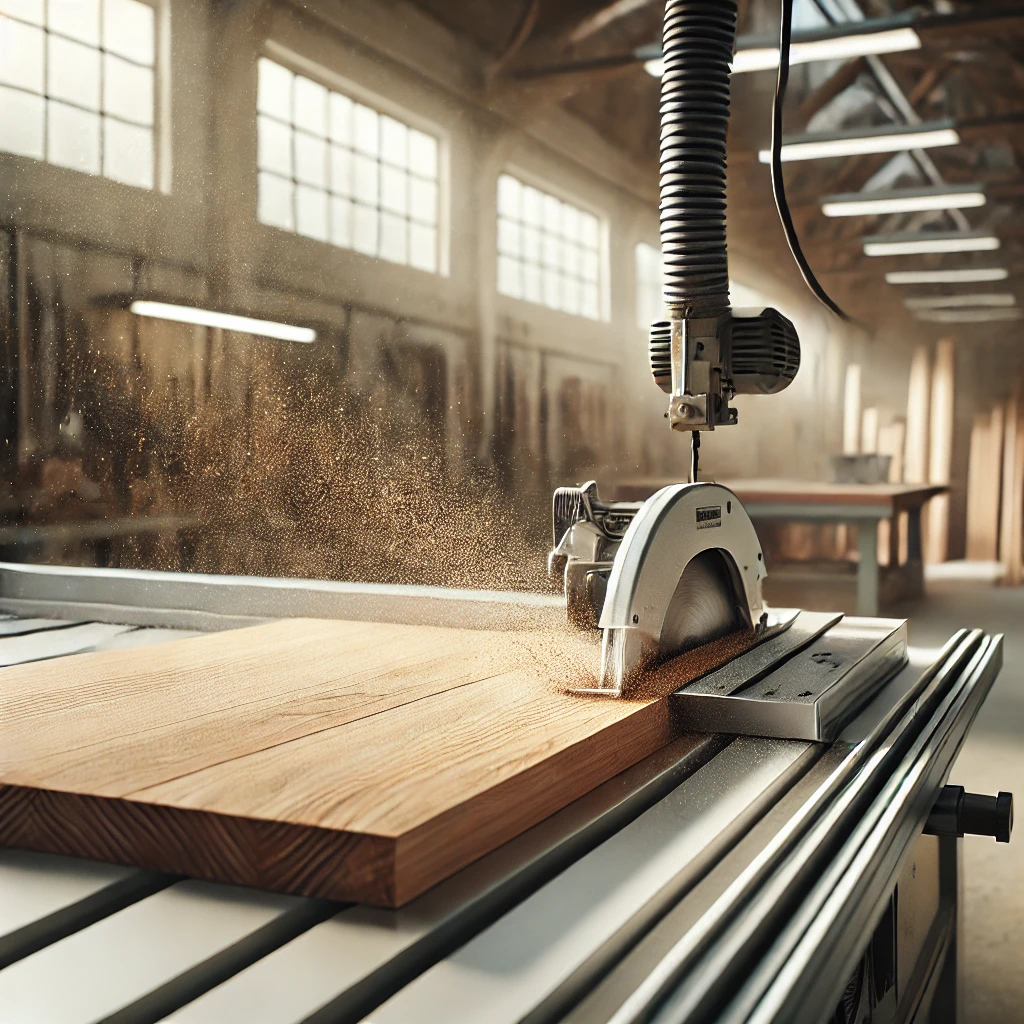
The width of your saw blade’s kerf impacts virtually every aspect of your woodworking experience:
- Material efficiency: Thinner kerfs mean less wood is converted to sawdust, allowing you to get more usable pieces from your stock.
- Motor strain: Thinner blades require less power to cut through material, reducing the load on your saw’s motor.
- Precision: In detailed work where every millimeter counts, thin kerf blades allow for more exact cuts and joints.
- Specialized applications: When working with expensive exotic hardwoods or thin veneers, minimizing material loss becomes economically significant.
The difference between standard and thin kerf blades might seem negligible at first glance—just a millimeter or so—but experienced woodworkers understand that precision at this scale often separates amateur work from professional results.
Benefits of Using Thin Kerf Table Saw Blades
Now that we understand what kerf width is, let’s explore the tangible benefits these specialized blades bring to your workshop.
Material Conservation and Efficiency
One of the most compelling reasons woodworkers choose thin kerf blades is material conservation. When working with expensive hardwoods like walnut, cherry, or exotic species that can cost $20 per board foot or more, every bit of saved material translates directly to cost savings.
Consider this practical example: If you’re ripping a series of 1/4″ strips from a board using a standard 1/8″ kerf blade, you’re essentially converting one-third of your material to sawdust! Switch to a thin kerf blade at 3/32″, and you immediately reduce waste by 25%. Over the course of a large project—like cabinet making or flooring—this efficiency can save significant amounts of material and money.
Beyond the financial aspect, there’s also an environmental consideration. Using thin kerf blades means fewer trees harvested for the same amount of finished woodwork. For eco-conscious craftspeople, this reduced resource consumption aligns with sustainable woodworking practices.
Power Requirements and Energy Savings
If you’re working with a contractor-grade table saw or a smaller benchtop model, you’ll particularly appreciate the reduced power demands of thin kerf blades. Since these blades remove less material with each pass, they require less horsepower to maintain cutting speed and quality.
This benefit manifests in several ways:
- Reduced motor strain: Your saw works less hard, potentially extending its lifespan
- Lower amperage draw: Beneficial if your workshop operates on limited electrical service
- Less bogging down: Maintains consistent speed even through denser hardwoods
- Smoother operation: Often translates to cleaner cuts with less tear-out
I’ve personally noticed that my 1.75 HP contractor saw handles thick maple much more confidently with a thin kerf blade than with a full-kerf alternative. What might cause stalling or burning with a standard blade becomes a smooth, controlled cut with a quality thin kerf option.
Precision Cutting Advantages
Perhaps most important for fine woodworking is the precision advantage that thin kerf blades offer. When cutting joinery or working on intricate projects, the narrower cut line provides several benefits:
- More accurate splining: When cutting slots for decorative or structural splines
- Better fitting joints: Less material removal means tighter tolerances
- Reduced deflection: Properly tensioned thin blades can actually provide straighter cuts in some applications
- Less tear-out: The reduced cutting force often results in cleaner edges, particularly in cross-cutting operations
For furniture makers and cabinetmakers where precision directly impacts the quality and strength of joinery, these advantages make thin kerf blades an obvious choice for many operations.
Top Thinnest Kerf Table Saw Blades on the Market
With the benefits clearly established, let’s examine some of the thinnest and most effective kerf blades available today. I’ve categorized these by price point and intended use to help you find the perfect match for your needs.
Premium Options for Professional Woodworkers
For those who demand the absolute best performance and longevity, these premium thin kerf options deliver exceptional results:
Forrest Woodworker II Thin Kerf (WWII-TK) With a kerf width of just 0.091″ (2.3mm), the Woodworker II thin kerf version remains the gold standard for many professional shops.
Forrest WW09307100 Woodworker II 9-Inch 30 Tooth 5/8-Inch Arbor 3/32-Inch Kerf Circular Saw Blade
- Forrest Saw Blades dampener helps kill saw scream-whistle from a vibrating blade surface.
- Dampen out motor and belt vibrations from being transmitted up to the rim of the teeth.
- Greatly reduce cutting noise.
List Price :
Offer: 129.94
Go to AmazonWhat sets this blade apart is its hand-hammered tensioning and exceptional build quality. The C4 carbide teeth maintain sharpness through hundreds of cuts, even in abrasive materials like plywood and MDF. At around $130-150, it’s an investment, but one that typically pays dividends in cut quality and reduced sharpening frequency.
Freud Premier Fusion (P410T) Featuring a remarkable 0.091″ (2.3mm) kerf and Freud’s proprietary TiCo Hi-Density Carbide, this blade combines an ultra-thin profile with impressive rigidity. The unique “fusion” tooth design handles both ripping and crosscutting with equal precision, making it an excellent all-purpose blade.
Freud P410T: 10" Thin Kerf Next Generation Premier Fusion General Purpose Blade
- Advanced Fusion Trio Tooth Design – Features Fusion Trio Tooth Design, combining 30° Hi-ATB, double grind, and Axial Shear Face Grind for optimal polished finishes in both ripping and crosscutting applications.
- TiCo Hi-Density Carbide – TiCo Hi-Density Carbide ensures a sharper edge and superior finish on a variety of materials, providing durability and long-lasting performance.
- Laser-Cut Anti-Vibration Slots – Laser-cut anti-vibration slots reduce vibration and lateral movement during cuts, ensuring a crisp, splinter-free finish and extending blade life.
New starting from: 79.97
Go to AmazonThe vibration-dampening laser-cut slots help maintain stability despite its thin profile. Typically priced around $80-90, it offers premium performance at a slightly more accessible price point.
Ridge Carbide TS2000 With a 0.098″ kerf (still considered thin by industry standards), the TS2000 features C4 micrograin carbide teeth and exceptional hand tensioning. What makes this blade special is its remarkable flatness tolerance—essential for ultra-precise cuts. Though slightly thicker than some competitors, many woodworkers report that its superior construction results in cuts that feel and perform like even thinner kerfs. The premium price ($140-160) reflects its handcrafted quality.
Ridge Carbide TS2000 Super Table Saw Blade 10" 40 Tooth ATB/R .125 Kerf 5/8" Arbor
- Feeds easily when used for moderate rips and crosscuts on a table saw.
- Raker tooth design for nearly a flat bottom cut.
- Smooth rip and cross cuts which eliminates the need for sanding.
New starting from: 149.00
Go to AmazonBudget-Friendly Thin Kerf Blades
Not everyone needs or can justify premium pricing. Fortunately, several manufacturers offer thin kerf blades that deliver excellent performance without breaking the bank:
Diablo D1040X With a 0.098″ kerf width, Diablo has created an accessible thin kerf option that performs admirably in most applications. The perma-shield non-stick coating reduces pitch buildup, while the laser-cut stabilizer vents minimize vibration. At around $40-50, it delivers impressive performance for occasional to regular use. The 40-tooth configuration makes it versatile enough for both ripping and crosscutting operations in most softwoods and hardwoods.
Diablo General Purpose Saw Blade for Wood – 10" Diameter, 40 ATB Teeth, 5/8" Arbor, .098" Kerf, 15° Hook Angle, .071" Plate, 7000 Max RPM – D1040X
- High-Performance TiCo Carbide – Ensures a sharp and durable cutting edge, designed for both rip cuts and crosscuts in various wood materials.
- Perma-SHIELD Non-Stick Coating – Protects the blade from heat, gumming, and corrosion, extending the blade’s life.
- Super Thin Laser Cut Kerf – For fast, durable, and clean cuts, good for your remodeling and demolition needs.
New starting from: 34.00
Go to AmazonIRWIN Marples 1807368 Featuring a 0.094″ kerf width, this 50-tooth combination blade offers excellent value around the $50 mark. The precision-ground teeth feature an alternate top bevel design that excels in crosscutting while still performing acceptably for ripping operations. The heat-resistant coating helps maintain cutting performance even during extended use, addressing a common concern with more affordable thin kerf options.
Irwin Tools IRWIN Marples 10-Inch Miter/Table Saw Blade, ATB, 50-Tooth (1807368)
- Designed for General Purpose cutting on a Table Saw or Miter Saw
- Alternate Tooth Bevel with Racer Tooth for knife like cuts and racer tooth for smooth finish
- Extra Sharp oversized carbide teeth are re-sharp enable for long life
New starting from: 56.36
Go to AmazonOshlun SBW-100080 At just 0.091″ kerf width, this 80-tooth blade is one of the thinnest in the budget-friendly category. Designed primarily for fine crosscutting in hardwoods and plywood, it features C4 micrograin carbide teeth that maintain sharpness surprisingly well for a blade in the $30-40 range. While not ideal for heavy ripping tasks, it excels in precision trimming and finish work.
Oshlun SBW-100080 10-Inch 80 Tooth ATB Fine Finishing Saw Blade with 5/8-Inch Arbor
- Copper Plugged Expansion Slots
- Professional Grade Carbide
- Tensioned And Hardened Steel Plate
New starting from: 56.11
Go to AmazonBest Value Picks for Hobbyists
For weekend warriors and casual woodworkers seeking the thin kerf advantage without significant investment, these options deliver the best value:
DEWALT DW7140PT With a 0.094″ kerf, this 40-tooth general purpose blade offers remarkable performance considering its approximately $25 price point. The computer-balanced plate reduces vibration, while the resin-filled expansion slots help maintain stability during temperature changes from extended cutting. While it won’t match premium options in longevity, it delivers clean cuts and efficient operation for occasional use.
DEWALT Table Saw Blade, 10", 40 Tooth, with Fine Finish, Ultra Sharp Carbide (DWA11040)
- UP TO 3X LIFE*
- Optimized Tooth Geometry Designed For Increased Accuracy
- Ultra Sharp Carbide for Clean Cutting
New starting from: 17.98
Go to AmazonConcord WCB1000C80 This ultra-thin 0.087″ kerf blade specializes in fine crosscutting operations at a budget price (approximately $30). The 80-tooth configuration with TCG (Triple Chip Grind) design makes it particularly suitable for laminate, melamine, and other man-made boards where chip-out is a concern. While not the most versatile option, it excels in its specialized application.
Technical Specifications to Consider
Beyond just finding the thinnest blade, several technical factors influence both performance and suitability for your specific needs.
Kerf Width Measurements Explained
When shopping for thin kerf blades, you’ll encounter various measurement conventions that can sometimes cause confusion:
Plate Thickness vs. Actual Kerf Width The blade’s plate thickness is just one component of the total kerf width. The actual kerf width includes the plate thickness plus the tooth set or carbide width. For example, a blade might advertise a 0.071″ plate thickness but have a total kerf width of 0.094″ once the carbide tooth width is factored in.
Industry Terminology
- Ultra-thin kerf: Generally under 0.080″ (2.0mm)
- Thin kerf: Typically 0.080″-0.100″ (2.0-2.5mm)
- Standard/Full kerf: Usually 0.100″-0.125″ (2.5-3.2mm)
When comparing blades, always look for the total kerf width rather than just the plate thickness to ensure you’re making accurate comparisons.
Tooth Count and Configuration
The number and arrangement of teeth on a thin kerf blade significantly impact its performance in different materials and cutting operations:
For Ripping Operations (Cutting with the grain)
- Lower tooth counts (24-30 teeth for a 10″ blade)
- Deeper gullets between teeth for chip evacuation
- Flat top grind (FTG) tooth profiles for efficient material removal
For Crosscutting (Cutting across the grain)
- Higher tooth counts (60-80 teeth for a 10″ blade)
- Alternate top bevel (ATB) or triple chip grind (TCG) tooth profiles
- Smaller gullets suitable for the finer dust produced
Combination Blades Many thin kerf blades are designed as combination or general-purpose blades, typically featuring:
- 40-50 teeth on a 10″ blade
- Alternating tooth configurations
- Gullet designs that balance chip evacuation with tooth support
For thin kerf blades specifically, tooth configuration becomes even more critical as the reduced plate thickness provides less support for the carbide teeth. This is why premium thin kerf blades often feature more sophisticated braze joints and carbide formulations to maintain tooth integrity despite the thinner backing.
Special Grinds for Specific Applications
Beyond standard tooth configurations, several specialized grinds are available in thin kerf formats for specific applications:
Hi-ATB (High Alternate Top Bevel) With bevel angles of 20° or more (compared to standard 10-15°), these blade configurations excel at cutting veneered plywood, melamine, and other materials prone to chipping. The steep alternating bevels shear the material cleanly, though this configuration tends to dull faster in abrasive materials.
Triple Chip Grind (TCG) Alternating between flat raker teeth and chamfered teeth, TCG blades excel at cutting hard materials like aluminum, brass, and hardened plastics. Several manufacturers offer thin kerf TCG configurations specifically for non-ferrous metals and composites.
Modified Triple Chip for Laminates Some specialized thin kerf blades feature modified TCG patterns with additional grind angles specifically designed for double-sided laminates and melamine-faced boards. These specialized grinds minimize chip-out on both the top and bottom faces simultaneously.
Potential Drawbacks and Limitations
While thin kerf blades offer numerous advantages, they’re not without limitations. Understanding these potential drawbacks helps ensure you choose the right blade for your specific applications.
Stability Concerns with Ultra-Thin Blades
As blade thickness decreases, several physical challenges emerge:
Deflection Under Load Physics dictates that thinner plates have less resistance to bending forces. During cutting operations, particularly in dense hardwoods or when feed rate is too aggressive, ultra-thin blades may deflect slightly. This deflection can manifest as:
- Burning on cut surfaces
- Wavy or inconsistent cut lines
- Difficulty maintaining perfectly square edges in thick stock
Resonance and Vibration Thinner plates have different harmonic properties and may be more prone to vibration at certain speeds. Premium manufacturers address this through:
- Laser-cut anti-vibration slots
- Copper or resin-filled expansion joints
- Computer-balanced plate designs
Tensioning Requirements Maintaining proper tension across the entire blade becomes more challenging as thickness decreases. This is why hand-tensioned premium blades often outperform mass-produced options in the ultra-thin category—each blade receives individual attention to tension distribution.
For these reasons, woodworkers tackling demanding applications like thick hardwood ripping might find that a moderately thin kerf blade (around 0.094″) offers the best balance between material savings and cutting stability.
Material Compatibility Issues
Certain materials pose specific challenges for thin kerf blades:
Abrasive Engineered Materials Products like MDF, particle board, and some plywoods contain adhesives and fillers that accelerate tooth wear. While thin kerf blades will cut these materials, expect:
- More rapid dulling of cutting edges
- Potential for increased heat buildup
- Greater likelihood of pitch accumulation on teeth
Very Dense Exotic Hardwoods Some tropical hardwoods like ipe, cumaru, and purpleheart are extremely dense (sometimes sinking in water). When cutting these materials:
- Thin kerf blades may experience more deflection
- Heat buildup can be problematic
- Slower feed rates become necessary
Wet or Resinous Woods Green lumber or resinous species like pine present challenges:
- Pitch accumulation occurs more quickly on teeth
- Sideways pressure from internal stresses may increase blade deflection
- Expansion/contraction during cutting can pinch thin blades more readily
In these challenging materials, slightly thicker thin kerf blades (0.094-0.098″) often provide better results than ultra-thin alternatives.
Maintenance and Care for Thin Kerf Blades
Proper maintenance becomes even more critical with thin kerf blades, as their reduced mass leaves less room for error in terms of cleaning and handling.
Cleaning and Storage Best Practices
Regular Cleaning Routine Thin kerf blades benefit greatly from frequent cleaning:
- Remove pitch and resin buildup before it hardens completely
- Use purpose-made blade cleaners or simple solutions like Simple Green
- Avoid soaking blades for extended periods, as this can affect adhesives in expansion slots
- Clean both the teeth and the plate body, as debris on either can affect cutting performance
Proper Storage Methods Between uses, thin kerf blades require careful storage:
- Store flat to prevent warping
- Use individual blade sleeves or a purpose-made blade storage system
- Avoid stacking blades directly against each other without protection
- Keep in a climate-controlled environment when possible to prevent rust
Handling Considerations The reduced thickness makes these blades somewhat more vulnerable to damage:
- Avoid dropping, as impact can affect tensioning or tooth alignment
- Don’t force blades onto arbors that don’t fit properly
- Be particularly careful with tooth edges, as repairs are more challenging on thin kerf configurations
When to Replace Your Thin Kerf Blade
All blades eventually require replacement or resharpening. With thin kerf blades, watch for these specific indicators:
Performance Indicators
- Increased burning along cut edges
- Rising pitch of blade sound during operation
- Noticeably increased feeding resistance
- Cut surfaces requiring more sanding than when the blade was new
Visual Inspection Points
- Visible flattening of carbide cutting edges
- Discoloration from heat along the plate (usually blue tinting)
- Any signs of micro-cracks in carbide teeth
- Tooth damage or chipping
Resharpening Considerations Thin kerf blades can typically be resharpened 3-5 times, though this varies by brand and model. When considering resharpening:
- Each resharpening removes a small amount of carbide, eventually affecting cutting performance
- Professional resharpening services with experience in thin kerf blades often deliver better results than general sharpening services
- The thinner plate provides less support for the teeth, making proper resharpening technique especially important
Most premium thin kerf blades remain economical even when factoring in periodic professional resharpening, often costing $25-35 per service while restoring like-new cutting performance.
Conclusion: Is the Thinnest Kerf Blade Right for You?
After exploring the world of thin kerf table saw blades, the question remains: is the absolute thinnest option the right choice for your workshop?
The answer depends largely on your specific priorities and working conditions. If you frequently work with expensive hardwoods, have a table saw with limited power, or specialize in fine furniture with precise joinery, a quality thin kerf blade likely represents an excellent investment. The material savings alone often justify the cost for regular woodworkers.
However, if you primarily cut construction lumber, frequently rip very thick stock, or occasionally cut slightly warped materials, you might find that moderately thin blades (around 0.094″-0.098″) offer a better balance of efficiency and stability than the absolute thinnest options.
Remember that blade quality matters tremendously—a premium thin kerf blade will typically outperform a budget standard kerf blade in most applications. Factors like carbide quality, tensioning, and overall manufacturing precision often impact performance more than small differences in kerf width.
Whatever your specific woodworking focus, today’s market offers thin kerf options for virtually every application and budget. By understanding the nuances of these specialized tools, you can make informed decisions that enhance both your craftsmanship and your workshop efficiency.
FAQs About Thinnest Kerf Table Saw Blades
1. Will using a thin kerf blade void my table saw’s warranty?
Most major table saw manufacturers now explicitly support the use of thin kerf blades. However, ultra-thin specialty blades (under 0.080″) might not be recommended for all saws. Always check your owner’s manual or contact the manufacturer if you’re uncertain. Generally, saws manufactured in the last decade are designed with the popularity of thin kerf blades in mind.
2. Can I use the same thin kerf blade for both ripping and crosscutting operations?
Yes, but with caveats. Combination or general-purpose thin kerf blades (typically 40-50 teeth on a 10″ blade) perform adequately for both operations in most woods. However, for production environments or premium results, dedicated ripping blades (24-30 teeth) and crosscut blades (60-80 teeth) will deliver superior results in their specialized applications. Many woodworkers find that having both types provides the best versatility.
3. Do thin kerf blades require special blade stabilizers?
While not absolutely required, many woodworkers find that blade stabilizers (sometimes called stiffeners) improve the performance of thin kerf blades, particularly in demanding cuts. These flat metal discs mount on either side of the blade and help prevent deflection. They’re especially beneficial when making deep cuts in dense hardwoods. However, using stabilizers will reduce your saw’s maximum cutting depth.
4. How much material can I actually save by switching to a thin kerf blade?
The savings are more significant than many realize. Switching from a standard 1/8″ (3.2mm) kerf to a thin 3/32″ (2.4mm) kerf reduces material waste by approximately 25%. On a project requiring 100 cuts, that equals about 8 inches of saved material. For expensive exotic hardwoods costing $20+ per board foot, these savings add up quickly. Additionally, the reduced energy consumption and decreased load on your saw’s motor represent additional long-term savings.
5. Are thin kerf blades more dangerous than standard blades?
When properly installed and used with appropriate technique, thin kerf blades are not inherently more dangerous than standard blades. However, their reduced mass means they might have slightly different kickback characteristics. Always use proper safety equipment including riving knives, blade guards, and push sticks regardless of blade type. Some woodworkers report that thin kerf blades actually reduce the likelihood of stalling in dense materials, potentially making them safer in certain situations by maintaining consistent cutting speed.
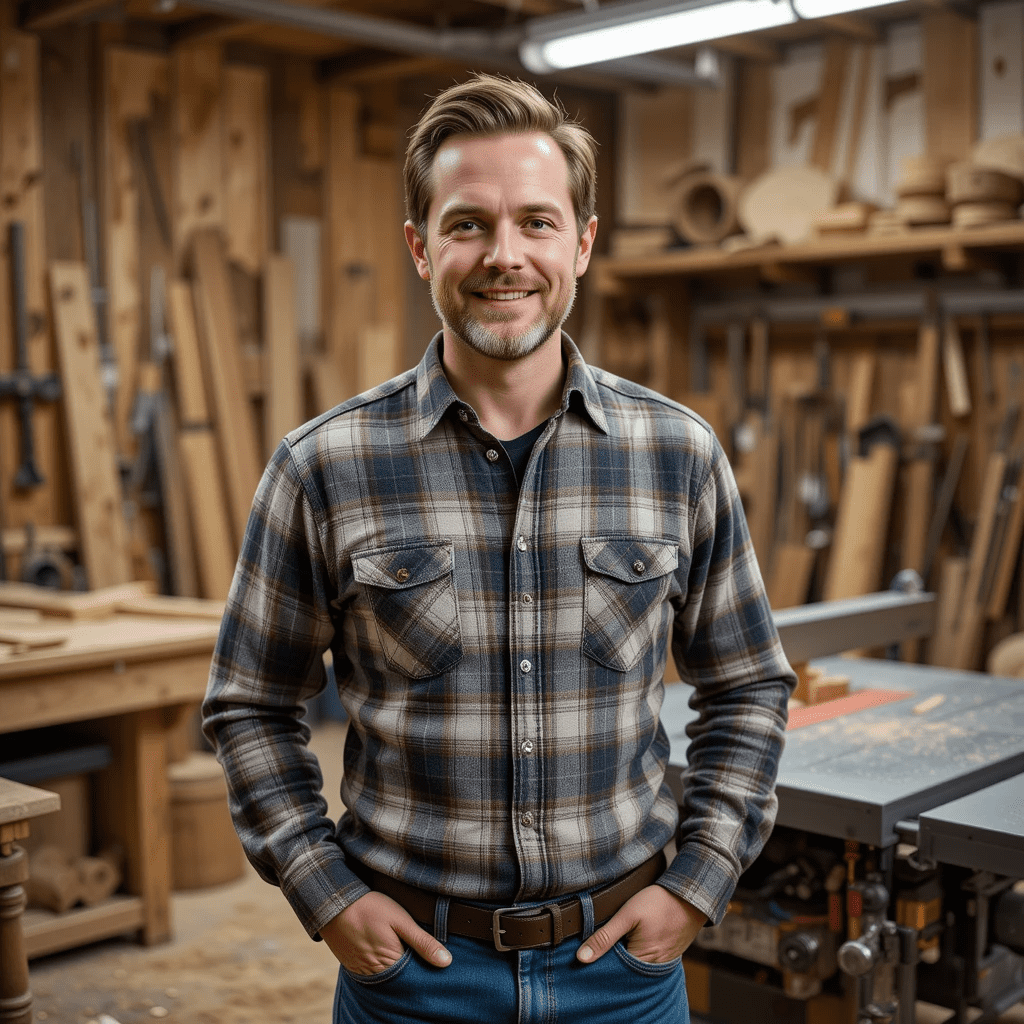
Finlay Connolly is a woodworking enthusiast and power tool specialist with over a decade of hands-on experience in the workshop. As the founder and lead writer at ProTableSawReviews.com, Finlay combines expert knowledge with real-world testing to help woodworkers, DIYers, and professionals choose the best tools for the job. With a sharp eye for detail and a passion for precision, Finlay is committed to providing trustworthy, practical advice backed by years of experience and research in the field. Whether you’re cutting dados or comparing fence systems, you can count on Finlay for honest, reliable reviews that make your next cut your best one.