Introduction to Cutting Plastic with a Table Saw
Why Cutting Plastic Requires Special Considerations
Cutting plastic with a table saw isn’t as straightforward as slicing through wood. While it might seem like a simple material, plastic behaves quite differently under the blade. Unlike wood, which generally has a consistent grain and texture, plastic can be dense, soft, or brittle, and each of these types reacts differently to the heat and friction generated during cutting.

One of the biggest concerns when cutting plastic is heat. As the saw blade spins at high speeds, it can cause the plastic to melt, warp, or fuse back together, especially if you’re using the wrong blade. That’s why the type of blade you choose matters. A standard wood blade can create too much friction, resulting in rough edges or even damaging the material. The goal is to get clean, smooth cuts without burning, chipping, or cracking the plastic—and for that, you need a blade that’s designed specifically for the job.
Another key consideration is the safety aspect. Plastic tends to chip or shatter when cut incorrectly, which can send small shards flying. This makes choosing the right blade not just about performance but also about keeping your workspace safe. The correct blade reduces the risk of kickback and produces cleaner cuts, which also helps when fitting pieces together for construction or fabrication projects.
So if you’re working on a DIY project, industrial build, or even just want to cut some acrylic sheets, understanding the fundamentals of plastic cutting with a table saw is essential. And it all starts with picking the right blade.
Common Challenges When Cutting Plastic
Plastic might seem like a forgiving material, but once you fire up the table saw, it has a mind of its own. Here are the most common issues that arise:
- Melting: The number one enemy. Heat buildup can cause the plastic to melt, making a mess on your blade and ruining your cuts.
- Chipping: Especially with harder plastics like acrylic or polycarbonate, you may see edges chip if the blade isn’t sharp or designed for plastics.
- Cracking: Thinner or more brittle plastics can fracture along the cut line, especially if the feed rate is too aggressive.
- Binding: If the blade gets too hot or if the plastic warps, it can bind, increasing the risk of kickback.
- Poor Finish: Jagged, cloudy, or scorched edges are signs that you’re using the wrong blade or the wrong technique.
Addressing these problems starts with your blade selection. The right tooth count, blade coating, and grind style can eliminate most of these headaches.
Understanding the Types of Plastic
Thermoplastics vs. Thermosetting Plastics
Let’s start with the basics: all plastics aren’t created equal. There are two main categories—thermoplastics and thermosetting plastics—and the type you’re cutting will determine what kind of blade you need.
- Thermoplastics soften when heated and harden when cooled. Common examples include acrylic (Plexiglas), polycarbonate (Lexan), PVC, and polyethylene. These are typically used in everything from windows to display cases. They’re the most commonly cut plastics on table saws.
- Thermosetting plastics, on the other hand, harden permanently after being heated once. Materials like epoxy resins or melamine fall into this category. They tend to be harder and more brittle, so the blade must be extremely sharp and ideally have a triple chip grind to prevent cracking.
The takeaway? Know your material. Thermoplastics can handle more aggressive cutting but are prone to melting, while thermosetting plastics require delicate handling and precise blades to avoid shattering.
How Plastic Type Affects Blade Choice

Different plastics behave differently when they’re cut. For instance, acrylic is prone to chipping but cuts cleanly with the right blade. Polycarbonate is tougher and more resistant to impact but tends to melt if you’re not careful with blade speed and feed rate.
Here’s how blade features align with plastic types:
- Acrylic: Needs a high-tooth-count blade with a sharp grind. TCG (Triple Chip Grind) is perfect.
- Polycarbonate: Requires a slower feed rate and a blade that stays cool—carbide-tipped blades work best.
- PVC and similar soft plastics: Can be cut with general-purpose blades, but a non-melt design is ideal.
Using the wrong blade is like trying to slice bread with a butter knife. You’ll get through it, but it won’t be pretty.
Key Features to Look for in a Table Saw Blade for Plastic
Tooth Count and Tooth Design
One of the first things to look at is the tooth count. The more teeth a blade has, the cleaner the cut—but there’s a catch. Too many teeth can also cause heat buildup, especially if you’re cutting thick plastic.
- 60 to 100 teeth: Best for fine cuts on plastics.
- Triple Chip Grind (TCG): The gold standard for cutting plastic. It alternates between a flat and trapezoidal tooth, reducing chipping and distributing force evenly.
Blades with alternate top bevel (ATB) or flat top grind (FTG) designs can also work, but they’re better suited for wood. For plastic, TCG is usually the safest bet.

Blade Material and Coating
Your blade should be carbide-tipped. Why? Carbide stays sharp longer, resists heat better, and produces cleaner cuts. Steel blades dull quickly and can cause burn marks on the plastic.
A non-stick or anti-friction coating also helps. These coatings reduce the chance of plastic sticking to the blade, which helps prevent melting and binding.
Blade Speed and Feed Rate Considerations
Speed kills—especially when it comes to cutting plastic. If the blade moves too fast or you push the material through too quickly, you’ll end up with melted edges or cracked sheets.
Look for blades that are designed for high RPM operations but also perform well at moderate feed rates. Controlled cutting is more important than raw power here.
Top Types of Table Saw Blades for Cutting Plastic
Triple Chip Grind (TCG) Blades
If you only remember one thing from this article, let it be this: TCG blades are your best friend for cutting plastic. The alternating flat and chamfered teeth make these blades perfect for producing clean, smooth cuts with minimal chipping and no melting.
- Why it works: TCG distributes cutting pressure and dissipates heat efficiently.
- Ideal for: Acrylic, polycarbonate, PVC, ABS, and other thermoplastics.
These blades are slightly more expensive, but they’re worth every penny if you want pro-quality results.
Carbide-Tipped Blades
Carbide tips add serious durability to your table saw blade. They last longer, resist wear, and stay sharper through more cuts.
- Why it works: Carbide handles heat better than steel, making it ideal for plastic.
- Ideal for: All plastic types, especially in high-volume environments.
They’re also a good general-purpose blade if you work with both wood and plastic regularly.
Non-Melt Blades and Their Benefits
Non-melt blades are specially engineered to reduce friction and heat buildup. They often come with a special coating and optimized tooth geometry.
- Why it works: These blades prevent plastic from fusing or gumming up.
- Ideal for: Thin plastics, laminates, or high-speed table saws.
They’re great for DIYers who don’t want to deal with sticky, melted plastic residue on their projects.
Top 5 Table Saw Blades for Cutting Plastic (with Reviews)
Freud LU94M010 10” Plastic Blade
Freud LU94M010: 10" Plastic Blade
- Specs: Arbor 5/8″, Diameter 10″, Grind MTCG, Hook Angle -3°, Kerf .110″, Plate .087″, Teeth 80
- Premium TiCo HI-Density Carbide Plastic Blend for Maximum Performance
- Modified Triple Chip Grind (MTCG) Tooth Design enables material to remain cool while cutting, eliminating melting
New starting from: 82.93
Go to AmazonThe Freud LU94M010 is hands-down one of the most trusted blades for cutting plastic. Why? Because it’s built for precision, clean cuts, and durability. With a triple-chip grind design and 80 teeth, this blade is engineered to handle plastic like a pro.
- Material: Carbide-tipped
- Tooth Count: 80 TCG
- Diameter: 10 inches
- Applications: Acrylic, Plexiglas, polycarbonate, PVC
This blade doesn’t just slice through plastic—it glides through it. Thanks to its Perma-SHIELD non-stick coating, it resists gumming and heat buildup, which is a game-changer when working with heat-sensitive materials. Plus, it’s one of the quieter blades on the market, so your shop won’t sound like a construction zone every time you make a cut.
Users consistently rave about the edge quality this blade delivers. It’s a bit on the pricey side, but you absolutely get what you pay for—professional-level cuts with minimal cleanup.
Diablo D1080N Non-Ferrous/Plastic Blade
Diablo Saw Blade for Medium Aluminum – 10" Diameter, 80 TCG Teeth, 5/8" Arbor, .094" Kerf, -5° Hook Angle, .071" Plate, 6000 Max RPM – D1080N
- Clean Cuts – Triple Chip Grind (TCG) Tooth Design delivers clean, burr-free finishes and virtually eliminates any need for rework, ensuring a superior cut every time. Ideal for cutting aluminum, copper, plastics, brass, and fiberglass.
- Impact Resistance – Built with Tri-Metal Shock-Resistant Brazing, allowing the blade to slice through metal materials while withstanding extreme impact, ensuring maximum durability on the job.
- Protection – Perma-SHIELD Non-Stick Coating offers protection against heat, gumming, and corrosion, keeping the blade clean and performing at its peak for longer periods.
New starting from: 43.76
Go to AmazonFrom the same manufacturer as Freud, Diablo’s D1080N blade is another beast when it comes to plastic cutting. Designed originally for non-ferrous metals like aluminum, this blade doubles up perfectly for plastics due to its excellent heat control and sharpness.
- Material: Carbide
- Tooth Count: 80 TCG
- Diameter: 10 inches
- Applications: Polycarbonate, acrylic, PVC, laminate
Its ultra-thin kerf allows for super smooth cuts with very little resistance, meaning less melting and cleaner edges. It’s ideal for thinner sheets of plastic where precision is a must. Whether you’re a hobbyist or a pro, this blade handles beautifully.
Tenryu PSW-255100AB Plastic Cutting Blade
Tenryu ML-255100AB 10" Carbide Tipped Saw Blade ( 100 Tooth ATAFR Grind – 5/8" Arbor – 0.118 Kerf)
- Sold on Amazon
New starting from: 145.5
Go to AmazonTenryu blades are a bit more under-the-radar, but they deliver elite performance, especially in the plastics and composites space. The PSW-255100AB is designed specifically for plastic, which means every detail—from tooth geometry to vibration dampening—is optimized for the task.
- Material: Carbide-tipped
- Tooth Count: 100 TCG
- Diameter: 10 inches
- Applications: Acrylic, polycarbonate, high-density plastics
What sets this blade apart is the polish-like finish it leaves behind. If you’re working on visible surfaces or items that don’t require sanding or flame polishing, this is a huge benefit. It’s not the cheapest option, but it’s certainly one of the most precise.
Oshlun SBP-100100 Plastic Saw Blade
Oshlun SBNF-100100 10-Inch 100 Tooth TCG Saw Blade with 5/8-Inch Arbor for Aluminum and Non Ferrous Metals
- Professional Grade C-1 Carbide
- Negative Hook Angle
- Triple Chip Tooth Grind
New starting from: 60.09
Go to AmazonFor those looking for a high-performance option without breaking the bank, the Oshlun SBP-100100 delivers solid value. It’s designed for plastics, acrylics, and PVC, and does a great job minimizing chipping and cracking.
- Material: Professional-grade carbide
- Tooth Count: 100 TCG
- Diameter: 10 inches
- Applications: Plastic sheets, corrugated plastic, ABS
It’s a reliable choice for DIYers who need something better than a wood blade but aren’t ready to drop top dollar on industrial-grade gear. It cuts clean, runs cool, and holds up well over time.
Concord Blades ACB1000T100HP Plastic Blade
The Concord ACB1000T100HP is a solid mid-range option. With its 100-tooth count and triple-chip grind, it’s perfect for cutting acrylics, plastics, and laminates with minimal edge cleanup.
- Material: Tungsten carbide
- Tooth Count: 100 TCG
- Diameter: 10 inches
- Applications: Acrylic, PVC, ABS, polycarbonate
Its anti-kickback design makes it safer for less experienced users, and it’s versatile enough to handle both plastics and soft metals. The blade runs cool and makes smooth, quiet cuts—something you’ll appreciate during long sessions.
How to Use a Table Saw to Cut Plastic Safely
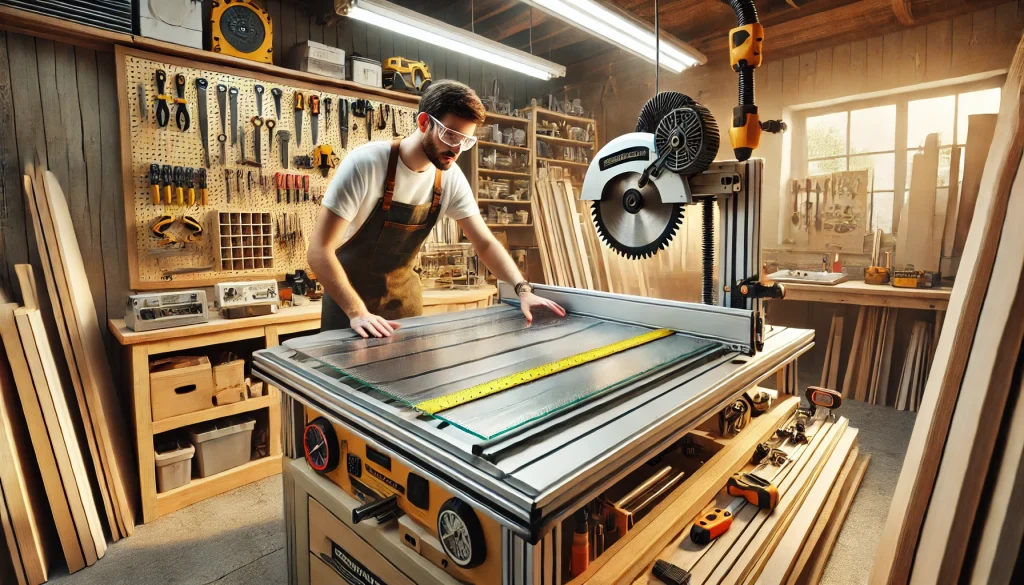
Preparing the Material
Before you even touch the power switch on your table saw, prep your plastic. Clean off any dust or residue that could affect the accuracy of your cut or clog your blade. Mark your cut lines clearly using a non-permanent marker. For best results, use painter’s tape along the line to reduce the chance of chipping.
You should also clamp the material if possible—especially for smaller pieces. This prevents shifting during the cut, which is one of the top causes of jagged edges or ruined panels. Finally, wear safety goggles, a dust mask, and hearing protection. Even though plastic dust isn’t as irritating as wood, it can still be harmful if inhaled.
Setting Up the Table Saw
First, make sure the table saw is fitted with a blade suitable for plastic. Set the blade height so it barely clears the thickness of the plastic sheet—no more than 1/4″ above the surface. This reduces the likelihood of chipping and helps with cleaner cuts.
Next, check your fence alignment to ensure straight cuts, and adjust your feed rate so you’re not pushing too hard or fast. The goal is a steady, consistent motion that minimizes heat buildup. Use featherboards or push sticks to guide the plastic safely, keeping your hands away from the blade.
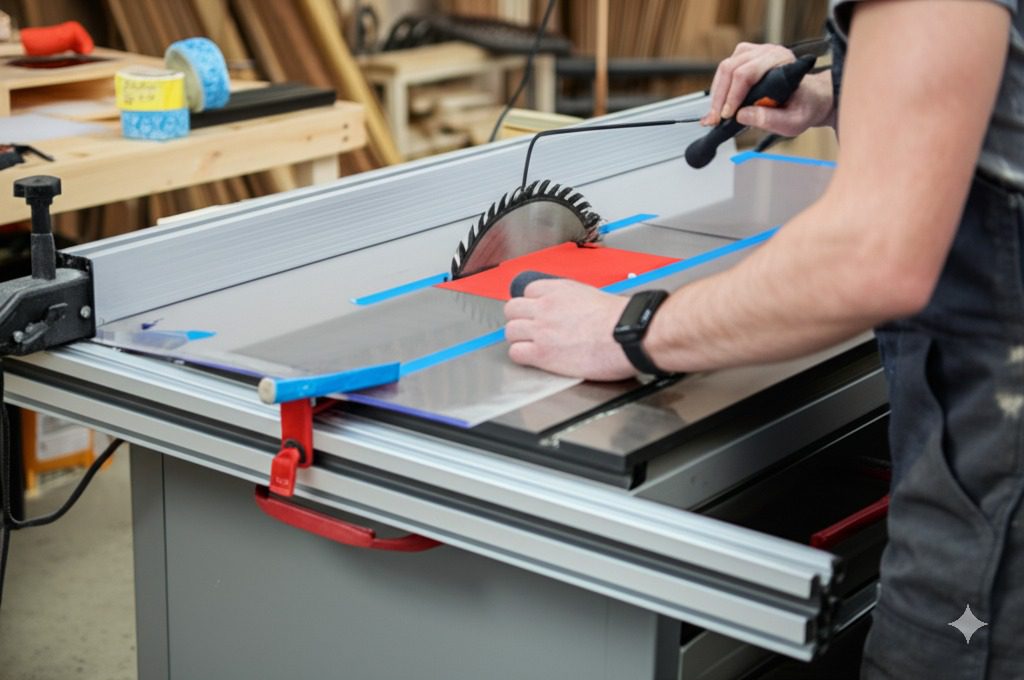
Safe Cutting Techniques
Cutting plastic is all about control. Use a moderate feed rate and avoid stopping mid-cut unless absolutely necessary. If you need to pause, back the material away slowly rather than stopping it in place—this helps prevent melting and blade marks.
Also, don’t force the plastic through the blade. Let the blade do the work. If you notice smoke, a burning smell, or hear a whine, slow down immediately—these are all signs that you’re cutting too fast or the blade is overheating.
Lastly, always stand to the side of the cutting path to avoid potential kickbacks, and double-check your blade guard and anti-kickback pawls are in place.
Tips for Getting Clean Cuts on Plastic
Avoiding Melting and Chipping
Melting is the bane of every plastic-cutting project. The friction between blade and material generates heat fast, and plastic is quick to warp or even fuse right back together along the cut. To avoid this, use a blade with a non-stick coating and a triple-chip grind tooth pattern, which reduces heat buildup.
Also, pay attention to your feed rate. Go too fast and you’ll chip; go too slow and you’ll melt. It’s all about balance.
Supporting the Workpiece
Proper support is key. Use a sacrificial board underneath the plastic to stabilize it during the cut. This not only helps reduce vibration (which causes cracks) but also ensures you don’t accidentally damage your saw table.
For larger sheets, support both the infeed and outfeed with roller stands or extension tables. This keeps everything level and steady as you push the material through.
Using Lubrication for Better Results
Some plastics, especially harder or thicker ones, benefit from a touch of lubrication. You don’t want anything greasy—just a light mist of water or a specialty cutting spray can help reduce friction and prevent melting.
If you’re cutting multiple sheets or thick material, this step can make a massive difference in the quality of your cuts.
Common Mistakes to Avoid When Cutting Plastic
Using the Wrong Blade
This is, without a doubt, the most common and costly mistake people make. Trying to cut plastic with a wood-specific blade or a dull utility blade will give you poor results—think melted edges, cracking, and even dangerous kickbacks.
The wrong blade type creates excessive friction, which heats the plastic to the point of softening or melting. Worse yet, it can gum up your blade and render it useless faster than you can say “replacement.” Always go for a blade specifically labeled for plastics, preferably with a triple chip grind and a carbide tip. It’s a simple switch that saves time, money, and frustration.
Cutting Too Fast or Too Slow
Finding the right cutting speed is an art. Many beginners push the plastic too fast through the saw, causing jagged, chipped edges. Others go too slowly, resulting in a melted mess.
Too fast, and the teeth grab too aggressively, pulling chunks out of brittle plastics like acrylic. Too slow, and the heat buildup starts to warp or fuse the plastic right at the blade. Always test your speed on a scrap piece before committing to the final cut. This small step can save your entire project from going up in smoke—literally.
Skipping Safety Gear
Even if plastic seems “softer” or “less risky” than wood or metal, skipping safety gear is a big no-no. Fragments of acrylic or PVC can chip off like glass and hit your face or eyes. Always wear safety goggles, hearing protection, and preferably a dust mask or respirator, especially if you’re cutting inside.
You should also use push sticks, featherboards, and clamps whenever possible. Table saws are powerful, and plastic can kick back just as violently as wood. Don’t let overconfidence turn into a trip to the ER.
Blade Maintenance Tips for Longevity
Cleaning the Blade Properly
Plastic tends to leave behind residue, especially if any melting occurs during cutting. This residue can build up between the teeth and along the blade body, which affects performance and increases heat with every subsequent use.
To clean your blade, soak it in a non-corrosive cleaning solution (like a diluted degreaser or a specialty blade cleaner) for 10–15 minutes. Then, use a brass wire brush or toothbrush to gently scrub away any buildup. Be thorough but careful—cleaning keeps your cuts sharp and your blade spinning smooth.
Avoid harsh chemicals or wire wheels that can strip the blade’s protective coating. Always dry the blade thoroughly before storage to prevent rust or corrosion.
Sharpening Frequency
Even the best carbide-tipped blade will dull over time, especially if used frequently on hard plastics. Dull blades not only produce poor cuts—they also increase the risk of melting, kickback, and injury.
A good rule of thumb: if your blade starts producing more burn marks, smoke, or rough edges than usual, it’s time to sharpen it. You can do this professionally for a relatively low cost, or use a carbide sharpening tool if you’re confident in your skills.
Try to log how often you use the blade and schedule sharpening based on hours of use or visible wear.
Storing the Blade Safely
Proper storage goes a long way in extending your blade’s life. Store blades in a dry, temperature-stable environment. Use wall-mounted holders or blade storage cases to keep them organized and protected from damage.
Avoid stacking blades directly on top of each other. This can dull the teeth and chip the carbide tips. Even a small nick can compromise the blade’s balance and effectiveness. Treat your blades like you would a chef’s knife—sharp, clean, and always stored with care.
When to Replace Your Table Saw Blade
Signs of a Dull or Damaged Blade
No matter how careful you are, every blade has a lifespan. Knowing when it’s time to replace your blade instead of sharpening it is key to maintaining cutting quality and safety.
Look for these signs:
- Burn marks on your cuts
- Increased effort to push the plastic through
- Excessive melting or chipping
- Audible changes in cutting noise (a dull, dragging sound)
- Visual damage like missing teeth, chips, or warping
If you’ve cleaned and sharpened the blade but still see poor results, it’s probably time to invest in a new one.
Performance Drops to Watch For
You know your tools. If your cuts aren’t as smooth as they used to be or if you find yourself making more passes to clean up edges, your blade may be reaching the end of its usable life.
Another clear signal? If the saw starts to bog down or vibrate during cuts, especially in materials it used to handle with ease, the blade could be warped or off-balance. Don’t risk it—replace it before it becomes a hazard.
Premium blades may cost more upfront, but they usually offer longer lifespans and better performance throughout. If you’re cutting plastic regularly, it’s worth keeping a fresh backup on hand at all times.
Cost vs. Performance: Are Premium Blades Worth It?
Budget vs. Professional Use
If you’re just doing a one-off project, a budget-friendly blade might get the job done. But if you work with plastic regularly—say, in signage, fabrication, or DIY electronics—a premium blade is a smart investment.
Budget blades tend to dull faster, cause more chipping, and require more cleanup after the cut. In contrast, premium blades (like Freud or Tenryu) offer polished edges, cooler cuts, and longer service life. They also reduce waste and time, which matters whether you’re a business owner or just value your free time.
Think of it like this: a budget blade might save you $20 upfront, but if you ruin two sheets of acrylic at $30 each, was it really worth it?
Long-Term Value and Durability
The best part about premium blades is consistency. Cut after cut, they deliver the same clean results. That means less sanding, polishing, or recutting. Over time, this saves both material and labor costs.
Durability also means fewer blade swaps and fewer trips to the store. While budget blades may need replacement after 10–20 cuts, top-tier blades can go for 50–100+ if maintained properly. Factor in the reduced frustration, improved safety, and cleaner cuts—and premium blades more than pay for themselves.
Conclusion
Cutting plastic with a table saw may seem intimidating at first, but with the right blade and proper technique, it becomes smooth, efficient, and even satisfying. Whether you’re slicing through acrylic sheets for a home project or running dozens of cuts for commercial applications, the blade you choose plays a critical role in the quality and safety of your work.
From TCG (Triple Chip Grind) blades that minimize chipping to carbide-tipped workhorses that power through thick plastics without melting, there’s a perfect blade out there for every need. Pair your blade with the right cutting speed, setup, and safety practices, and you’ll get clean, professional-looking results every time.
So next time you’re working with plastic, skip the guesswork. Choose a blade built for the job, take your time with the cut, and always prioritize safety. Your projects—and your fingers—will thank you.
FAQs
Can I use a wood blade to cut plastic?
Technically, yes—but it’s not recommended. Wood blades can cause melting, chipping, and even cracking in plastic. Use a blade specifically designed for plastic, ideally one with a triple chip grind and carbide tips.
How do I prevent the plastic from melting during the cut?
Use a non-melt blade with a low-friction coating, slow your feed rate slightly, and avoid stopping mid-cut. Keeping your blade sharp and clean also helps minimize heat buildup.
What’s the safest blade for a beginner?
A high-tooth-count TCG blade like the Oshlun or Diablo models is great for beginners. Pair it with proper guides, a push stick, and wear all safety gear. Don’t rush your cuts.
Do I need a special lubricant when cutting plastic?
Not always, but for thicker or tougher plastics, a light mist of water or a plastic-safe cutting lubricant can help reduce friction and improve cut quality.
What’s the ideal RPM for cutting plastic?
Most plastic-compatible blades are designed to operate well at standard table saw RPMs (3,000–5,000). The key is to match your blade type with the material and keep the feed rate steady.
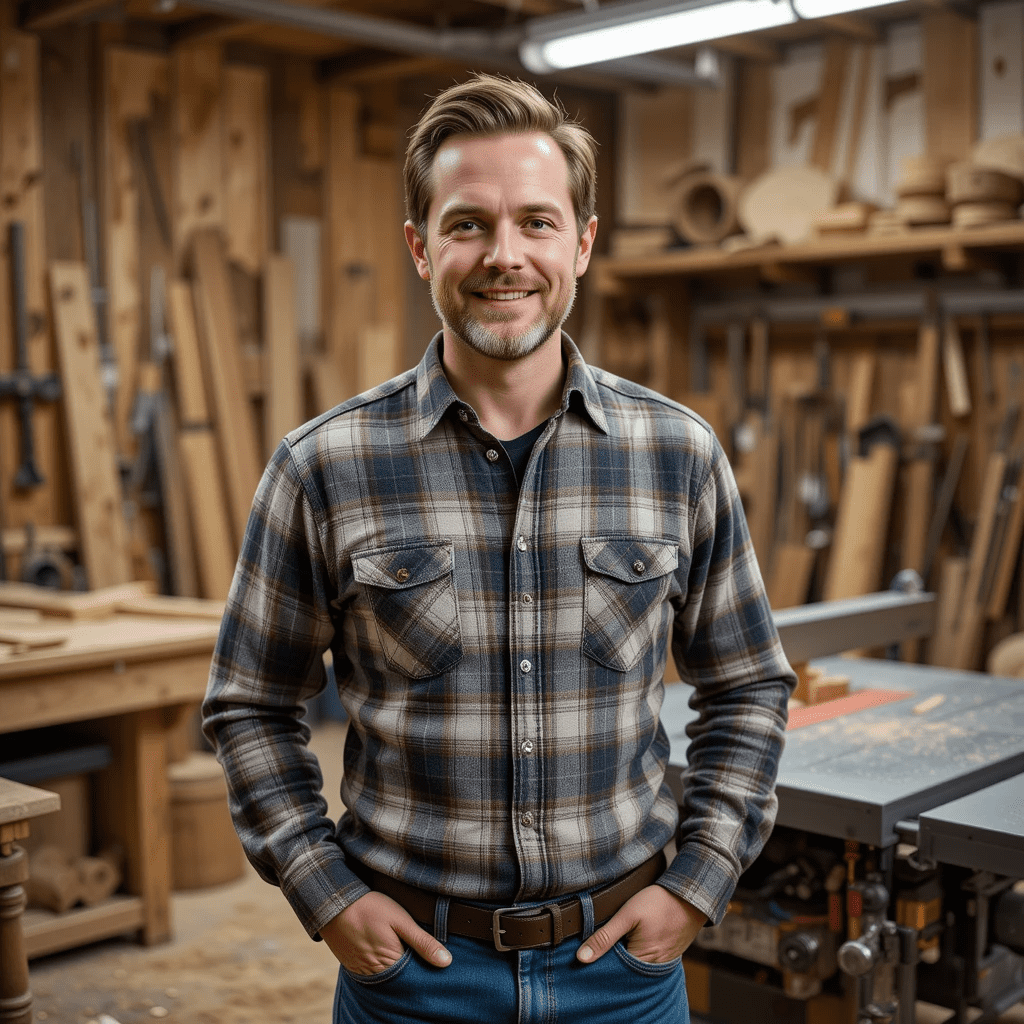
Finlay Connolly is a woodworking enthusiast and power tool specialist with over a decade of hands-on experience in the workshop. As the founder and lead writer at ProTableSawReviews.com, Finlay combines expert knowledge with real-world testing to help woodworkers, DIYers, and professionals choose the best tools for the job. With a sharp eye for detail and a passion for precision, Finlay is committed to providing trustworthy, practical advice backed by years of experience and research in the field. Whether you’re cutting dados or comparing fence systems, you can count on Finlay for honest, reliable reviews that make your next cut your best one.